Process flow of organic fertilizer production line how to select organic fertilizer granulator
2025/07/01
The fermentation link of organic fertilizer production is mainly to provide strains, auxiliary materials and temperature and humidity environment conducive to waste fermentation, so as to promote the rapid fermentation of livestock and poultry waste, and then treat it through certain granulation methods, and finally get organic finished products rich in nitrogen, phosphorus, potassium and other plant nutrients.
During the operation of the organic fertilizer production line, the organic materials obtained by fermentation in the reaction tower, urea, ammonium, etc. are added into the disc mixer in a specific ratio, and then sent to the granulator for granulation after being evenly mixed. In the granulator, the materials form a mechanical fluidized bed at a certain speed, during which an appropriate amount of steam is added to provide corresponding heat and moisture for the granulation process, and then an appropriate amount of circulating washing liquid obtained by subsequent tail gas washing is sprayed to promote the agglomeration of materials into particles.
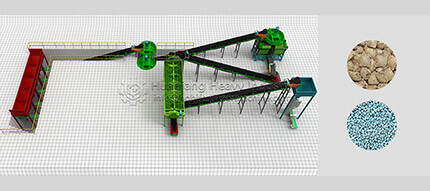
The granulating and forming system of the organic fertilizer granulator is to mix the crushed ingredients and make the materials into particles. The granulator with agitated teeth can be used for granulation, which has the advantages of fast granulation speed and high efficiency. The disadvantage is that the forced extrusion force is small, which needs to be matched with high-power crushing equipment. The flat mold granulator can also be selected. Its advantages are: wide adaptability of raw materials, especially suitable for organic substances: wide requirements for raw material density and raw material moisture, and raw materials do not need to be dried: the diameter of the pressing roller is large, and the template can be used in both positive and negative directions. The materials are evenly distributed in the compression chamber, with stable granulation, high particle forming rate, uniform appearance of finished particles and not easy to break: no water is added in the whole granulation forming process, Save the cost of subsequent particle drying: the fineness requirements of raw material crushing are not high. Granulating raw materials (after composting) generally do not need fine crushing, and fine stones can be directly crushed. Its disadvantage is the high maintenance cost.