Bio-organic fertilizer has high organic matter content, contains a large amount of elements such as NPK and trace elements, and metabolites of beneficial microorganisms. Bio-organic fertilizer is a high-quality commercial organic fertilizer. Organic fertilizer plant uses farm manure and crop straw as raw materials, uses high-temperature fermentation technology to remove pathogenic microorganisms, pests and their eggs from raw materials, and makes these wastes into bio-organic fertilizers with stable fertilizer efficiency and good quality, thus avoiding the pollution of the environment by these wastes and obtaining high-efficiency benefits. The construction of a bio-organic fertilizer production line is mainly the composting fermentation in the early stage and the processing of organic fertilizer in the later stage.
Raw material for bio-organic fertilizer production line
Ingredients: Livestock and poultry manure from farms
Supplementary materials: straw, mushroom chaff, agricultural by-products and food processing waste, organic waste, municipal sludge
Compost fermentation production processing
There are two commonly used fermentation methods of bio-organic fertilizer: compost fermentation on flat land, fermentation in fermentation tank.
1) Compost fermentation on flat land
Animal manure, straw, rice husk and other materials are added to the fermentation agent, and evenly mixed and stacked. The best height is not more than 1.5 meters, and the length is variable, it is turned over every 2 days,. The windrow compost turning machine is a common mechanical turning machine in this fermentation mode. In order to speed up the fermentation, ventilation pipes can be laid at the bottom of the fermentation reactor to increase the oxygen content of the compost. The construction cost of this fermentation method is low in the early stage, the composting fermentation speed is relatively slow and the area is large.
2) Fermentation in fermentation tank
After mixing, the raw materials are put into the fermentation tank, and the water content is adjusted to 55-65%. The aerator can be laid at the bottom of the fermentation tank. The compost turning mahcine is turned over once a day. The materials in the fermentation tank can be batch-discharged, and a batch of compost is produced simultaneously with a batch of raw materials. The cured material basically realizes the harmlessness of the product and can be used as a processing raw material for the organic fertilizer production line.
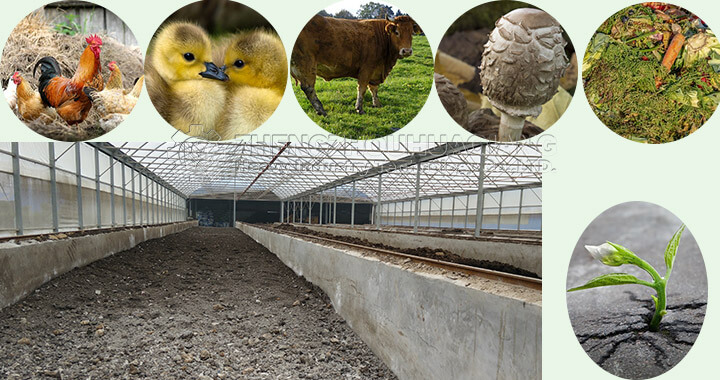
In the processing of organic fertilizer equipment, functional bacteria and other nutrients can be added to improve the performance and pertinence of fertilizer. The organic fertilizer production line processes the fertilizer powder into granule products, which avoids the disadvantages of poor appearance, inconvenient spreading, and unsustainable fertilizer effect of the powder product, and improves the quality of the organic fertilizer product.
Process steps of bio-organic fertilizer production line
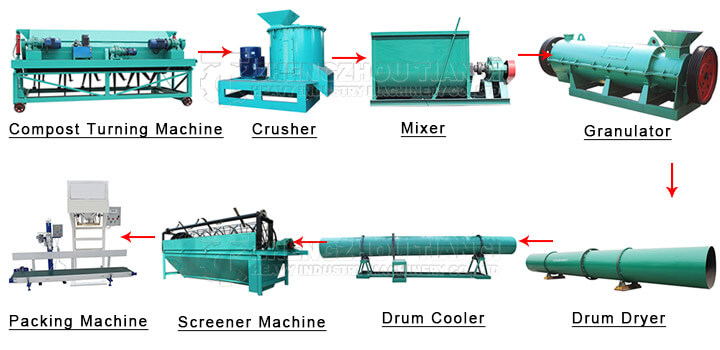
Crushing and mixing
Fermented compost is crushed into powder by the half-wet material crusher. These powder and other materials are mixed in the mixer. Finally, the compost is sent to the granulator through the conveyor machine for granulation.
Granulation
The organic fertilizer powder is fed into the organic fertilizer granulator by the conveyor, and the powder is granulated by the granulation process. The common organic fertilizer granulator includes disc granulator, new type organic fertilizer granulator, ring die granulator, etc. The corresponding granulator is selected according to the organic fertilizer production process.
Drying and cooling
The material conveyed from the granulator enters the drum dryer for drying. After drying, the material enters the cooling machine to complete the cooling of the material. During the drying and cooling process, a large amount of dusty and humid exhaust gases are produced, which are collected by the dust collector and re-discharged into the atmosphere.
Screening
After drying and cooling, the material directly enters the fertilizer screening machine. The screening machine screens out the qualified granules for packaging, and the remaining large granules and powder are returned to the fertilizer line for re-comminute and granulation.
Packing
Fertilizer packing machine packs fertilizer products quantitatively, and the packing bags are placed on conveyor belts and sewed automatically. Packaged products can be sold as commercial organic fertilizers.